Organization
Factories
Republic Technologies France has more than 25,000 square meters of production facilities in Perpignan distributed between two sites:
- The Orles production facility which is exclusive for cigarette paper manufacturing and smoking accessories.
- The Torremila facility, expanded in 2019, which produces e-liquids, optical products and provides logistics solutions.
The entire production area is continuously controlled in regards to temperature and humidity in order to guarantee the preservation and processing of the rolling paper. Republic Technologies France employs 400 people.
Our production teams are assigned to machines and product ranges, according to their expertise or specialization. Employees work in autonomous production groups, which allow them great flexibility in their work station.
We strongly value the ongoing training and development of our employees. They are trained to master the most modern manufacturing processes and methods. Our employees are expertly trained on our machines and high-tech equipment. We encourage internal promotion with training plans and personalized career development.
Republic Technologies France values its employee’s diversity, which is an asset to our success. Our policy is to recruit, train and promote our staff, in all positions, based on each employee’s abilities and skills. Republic Technologies France takes into account professional equality between men and women and the quality of life at the workplace. Every year, we calculate the equality index, which stood at 88* in 2022, in accordance with current methodology.
We are committed to promoting a healthy work environment that is favorable to the growth and development of our employees. In order to sustain the staff developmental efforts and fight against social exclusion, we are dedicated to improving our employees’ skills and training them regularly on their skills and development. We pay particular attention to the integration and career development of people with disabilities.
Our production organization is reactive and flexible to respond to any commercial requests. We have few hierarchical levels which allows direct and rapid communication.
We regularly update our industrial procedures and practices with an ongoing improvement program. Wherever and whenever possible, we apply methodologies like Lean manufacturing, Kaisen, and just-in-time. We practice FMAE for our technical developments and continuously improve our GMP: Good Manufacturing Practices.
* The gender equality index includes the following indicators : gender pay gap indicator 37/40, gender increase rate gap indicator 10/20, gender promotion rate gap indicator 15/15, percentage of female employees receiving a raise in the year following their return from maternity leave indicator 15/15, number of employees of the under-represented gender among the 10 highest earners indicator 5/10.
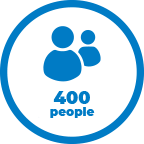

Software
We use the following production management systems:
- ERP : Enterprise Resource Planning – Integrated management software package that manages and coordinates all resources, information and functions of our activity, on our site and in the Republic Group companies. Its purpose is to facilitate the flow of information between all of our departments: finance, manufacturing, sales, and the rest.
- MRP : Material Requirements Planning – This planning system determines the needs and elements from finished product requests and current supply.
Our MRP system has 3 goals:
- To ensure we have enough raw materials for production and finish products for shipment to customers
- To optimize our inventory in order to maintain an optimal stock level
- To manage the industrial activity plan, delivery and purchase schedules
- SWb : Scheduling Workbench – Linked to the ERP, this software is used for finite capacity planning.
Advantages:
- Taking into account the process restrictions for order sequencing.
- Multi-level planning and synchronization (finished and ongoing products)
- CMMS : We maintain our machines using a specific software, accessible by the technician teams.
Our computerized maintenance management system, such as TPM (Total Productive Maintenance) or SMED. This allows us to increase our machines’ synthetic yield rates.
Logistics
In our warehouses and platform logistics, we implement the latest methods and practices :
- FIFO (First In, First Out) stock management, meaning that what goes in first, is processed first. All raw materials and finished products have their given placement, automatically assigned by the software. We log the barcode which identifies each product’s placement as well as its main characteristics.
- The forklifts are operated electronically in the warehouse. Automated driving makes it possible to be faster, prevent errors, and have a higher product density.
A logistical platform was created in 2011 to offer optimal service to our clients: greater reactivity and flexibility. There, we stock finished products and prepare global shipments.